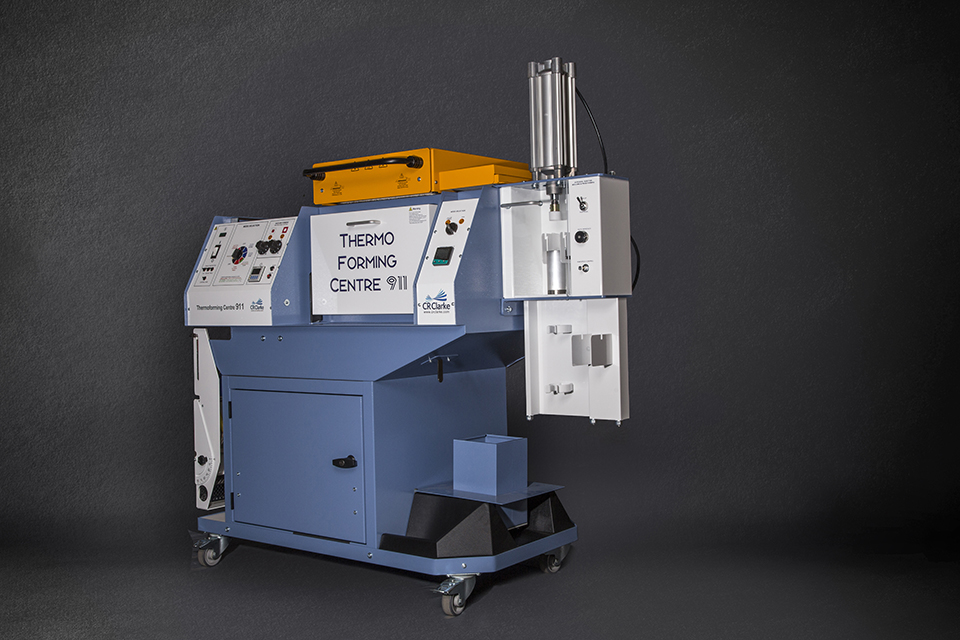
Vacuum Forming
Two sheet sizes, 305 x 305 and 305 x 152mm. Maximum mould height 115mm. The ceramic heater system hinges from over the oven to the heating position. A powerful vacuum pump ensures that high definition formings can be produced on materials up to 5mm in thickness.
Dome Blowing
A sheet of acrylic is heated in the fan circulated oven. Once softened, the user transfers the material to the dome blowing unit. Air from the vacuum pump is applied and the material is blown into a uniform hemisphere. The lack of a mould ensures that the finished item is optically clear and free from mould marks.
Dip Coating
A metal item is heated in the fan circulated oven. When hot, it is removed from the oven and dipped momentarily into the fluidised bath of plastic powder. A layer of powder adheres to the metal, and once removed the residual heat in the metal melts and flows the powder, forming a smooth protective coating that is ready to use as soon as it has cooled.
Plastic Welding
Plastic welding is the ideal process for materials that cannot be jointed using solvent cements, notably Polypropylene and PVC. The 911 incorporates an industrial quality, temperature controlled welding torch, enabling high-quality welds to be produced on these materials. The folding work table with angled stop allows materials to be set up accurately prior to welding.
Injection Moulding
A high-mass pot of thermoplastic powder is heated in the fan circulated oven. Once hot it is transferred to the injection moulding unit, where a pneumatic cylinder operated by the vacuum pump injects the molten material into the mould. Once cooled, the mould is split open and the completed item is removed.
Extrusion
A high-mass pot of thermoplastic powder is heated in the fan circulated oven. Once hot it is transferred to the injection moulding unit, where a pneumatic cylinder operated by the vacuum pump squeezes the material out through a narrow nozzle. As the material exits the extrusion nozzle it enters a cooling water tube, solidifying the material.
Voltage
Max Current
Sheet Size
Maximum Material Thickness
Maximum Mould Height
Dimensions (Packed)
Weight
230 50-60Hz
11 Amps
508 x 458mm
6mm
115mm
800 x 1400 x 900mm
152kg